Robotic Solution Laser Welding
As manufactured components become more complex, demand for precise assembly solutions arises. This issue compounds as plastic manufacturing produces more sophisticated parts. Laser welding provides a solution for these issues.
Laser welding also makes welding difficult materials such as copper and aluminum easier. Welding such materials are common in battery system manufacturing. Some facilities will manually weld materials using lasers. However, manufacturers commonly automate due to the high demand for precision.
Types of Laser Welding
Laser welding uses a high-powered laser to generate energy. The laser beam is focused to a fine point, concentrating the heat on a small area. This heat melts the material and allows the materials to bond–creating a weld. There are a few different types of lasers available for welding. Each has its benefits and shortcomings. Therefore, one must be aware of the options before making a purchase decision to avoid mistakes.
Gas (CO2) Lasers
Gas lasers send high-voltage, low-current energy through a gas medium to generate heat. While you can use other gasses (He/Ne, Ar/Kr), CO2 is the most common. Its popularity is due to its efficiency and high-power output.
However, CO2 lasers tend to be more expensive than other laser types. Additionally, they are sensitive devices. Crashes can throw off mirror alignment–a costly problem to fix.
Solid-State Lasers
Solid-state lasers use metals or crystals as a medium. Since they are solid-state, no material is consumed during operation. Additionally, these lasers can achieve minimal beam diameters compared to gas lasers.
However, thermal expansion can be an issue. If the medium gets too hot, the laser diameter can become distorted. Additionally, the power output is relatively lower than the CO2 models. This drawback can be problematic for specific materials. As a result, these lasers can struggle with thicker or deeper welds.
Semiconductor (Diode) Lasers
Semiconductor lasers are compact, lightweight, and efficient systems for welding. They don’t require active cooling systems, consume as much power as other options, and don’t use mirrors, making them a durable choice for rough environments.
However, these lasers cannot achieve the high power featured in CO2 models. Also, beam divergence is more prevalent with semiconductor lasers.
Industries for Laser Welding Robotics
Laser welding robots exist as a niche application within manufacturing. Very few industries require the unique characteristics and benefits of laser welding. However, for those industries, access to automated laser welding is vital.
Examples include:
- Automotive
- Aerospace
- Battery Production
- Electronics
- Healthcare
- Metals
- Plastics
Learn more
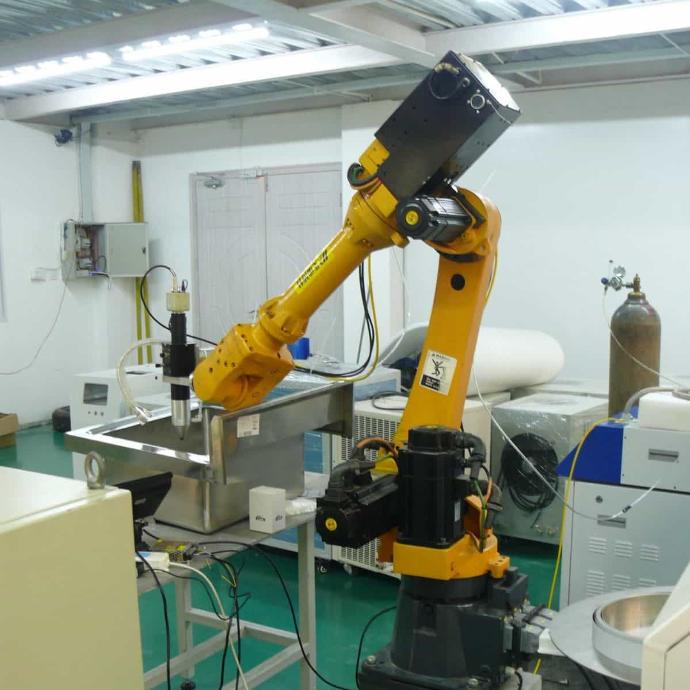
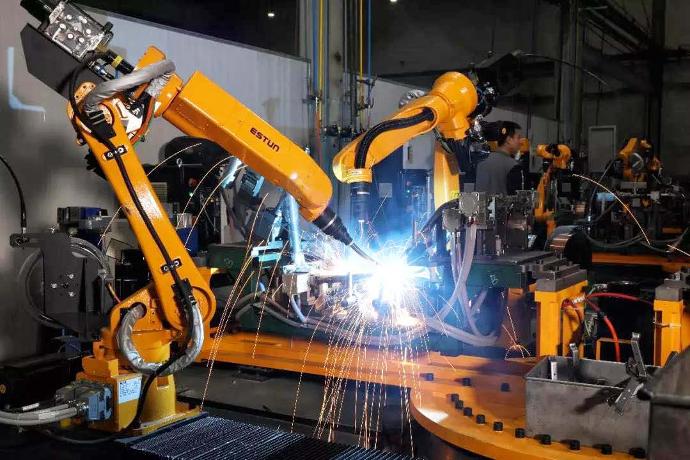
Six-Axis Robots
Six-axis robots offer a great mix of speed, reach, payload capacity, and reach. These robots can cover the vast majority of laser welding applications. They excel in small to medium-sized welding tasks. Their excellent range of motion helps them weld complex part geometries.
However, the six-axis robots’ shortcomings can limit their compatibility with larger jobs. For example, their reach is limited to a meter or two. Unfortunately, this is the case even for the biggest robots. However, manufacturers can reduce this shortcoming with the help of an RTU. A robot transfer unit (RTU) extends the reach of your six-axis robot. However, this is an expensive piece of hardware. In addition, RTUs carry separate integration costs and considerations.
To install this Web App in your iPhone/iPad press
and then Add to Home Screen.