Robot Industries RIDPLT1500AMR Mobile Robotic Depalletizing Cell with 3D Vision and AI
Robot Industries RIDPLT1500AMR Mobile Robotic Depalletizing Cell with 3D Vision and AI
Robotic Mobile Cells
- Environment recognition and intelligent navigation algorithm based on 3D point cloud
- Carriage size recognition and automatic planning of palletizing type
- Automatic planning of robot handling trajectory
- The whole line equipment of the conveyor line is stable and efficient
- The RICOB1500SMR is ideal for van truck and container depalletizing, with a single palletizing cycle time of up to 1000pc/h, allowing enterprises to exchange for efficient and convenient automated production at a lower cost, helping enterprises to develop rapidly.
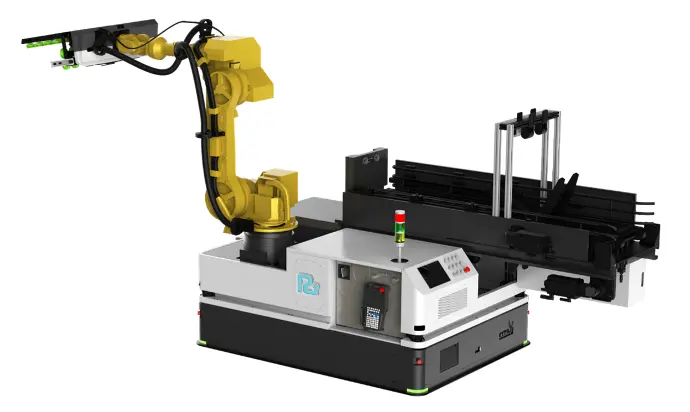
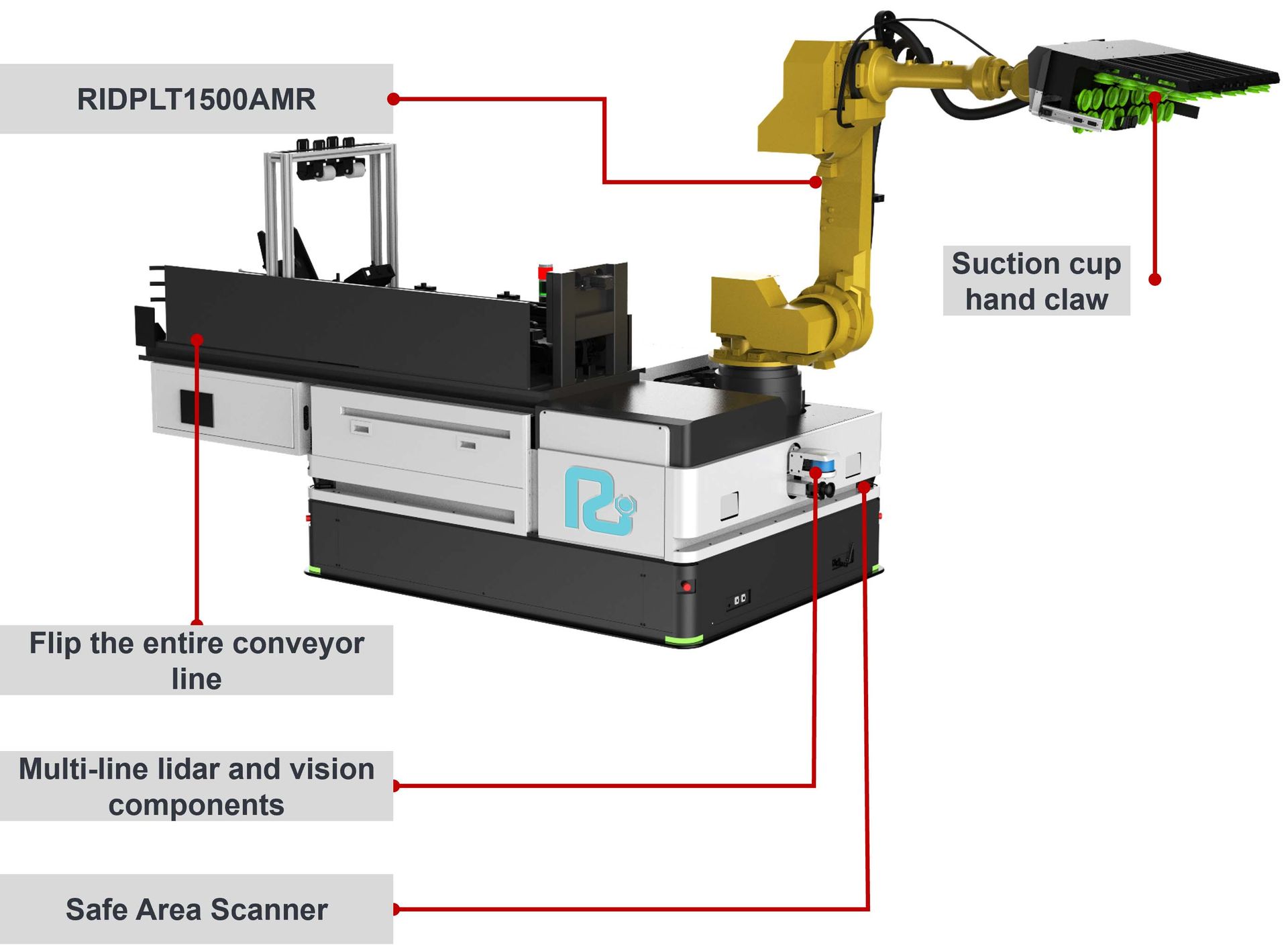
The equipment adopts SLAM and point cloud-based recognition and processing algorithms to intelligently identify the characteristics of the loading scene and automatically navigate in and out of the carriage. After the system enters the order information, it automatically generates a pallet plan for customers to choose. After the task is started, the whole process is automatically operated, completely replacing manual handling.
The system is designed for general logistics dock scenarios and does not require modification of the platform and carriages. Composite robot traction telescopic roller line direct deployment, Only the industrial three-phase electricity needs to be connected to the tail of the telescopic roller line, and the system is convenient and fast to import.
Product Advantages
Intelligent and automated
Intelligent navigation: The intelligent algorithm of 3D SLAM navigation based on 3D point cloud and scene feature recognition can realize automatic navigation in and out of the carriage.
Intelligent palletizing algorithm: Based on the planned palletizing type and recognized scene characteristics, the robot palletizing trajectory is automatically generated.
Safety protection: Real-time detection of the surrounding environment to effectively avoid equipment collision and fall. The equipment is equipped with multiple protections, which can stop the occurrence of harmful personnel in time.
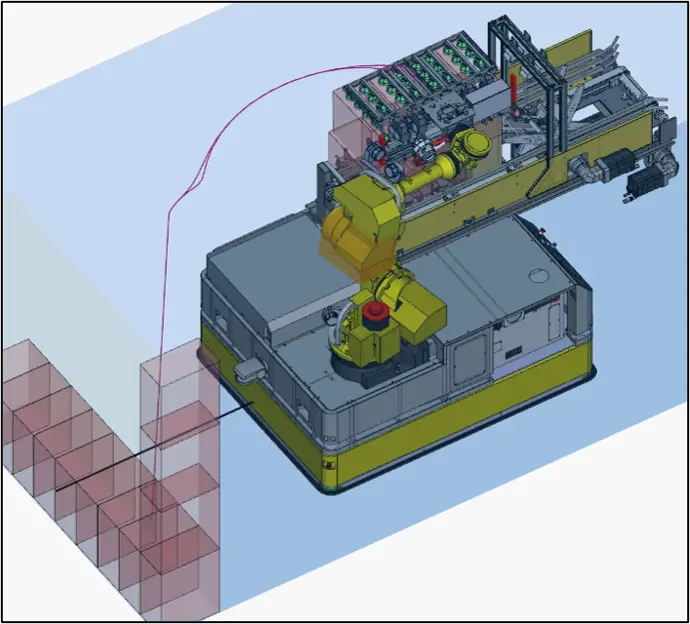
Compatible with a wide variety of goods, effective empty space, greater accessibility
Mixed product packaging: It can adapt to the mixed stacking type of products of different varieties and sizes, which is convenient for customers to distribute.
Multiple Placement Postures: The palletizing type adapts to the three placement postures of the goods, and can be combined with the stacking planning algorithm to efficiently use the space in the box.
Large palletizing range: the maximum stacking type is 2800mm high × 2900mm wide, covering the internal size range of traditional vans.
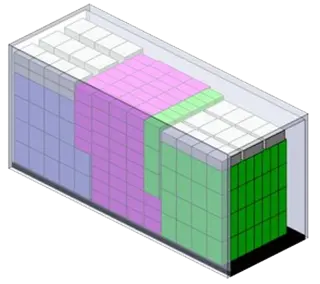
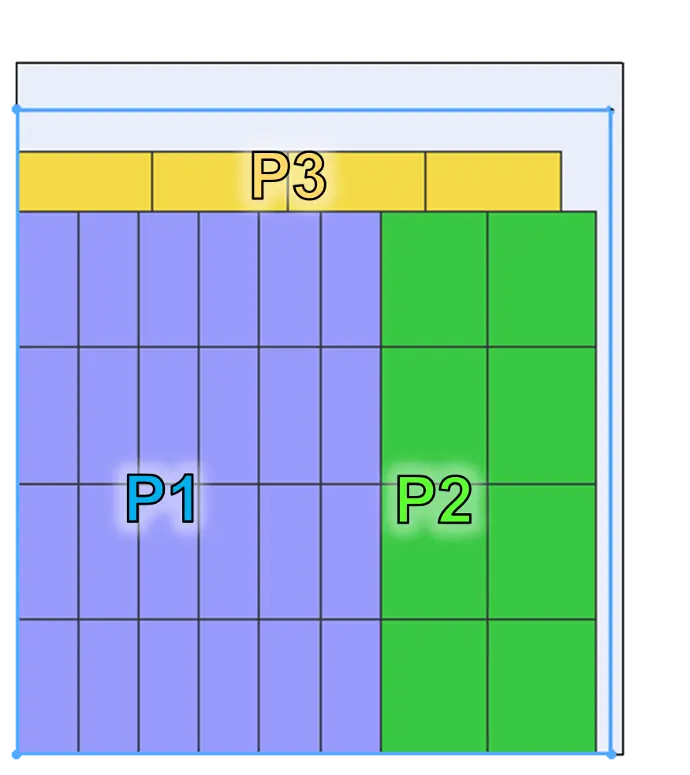
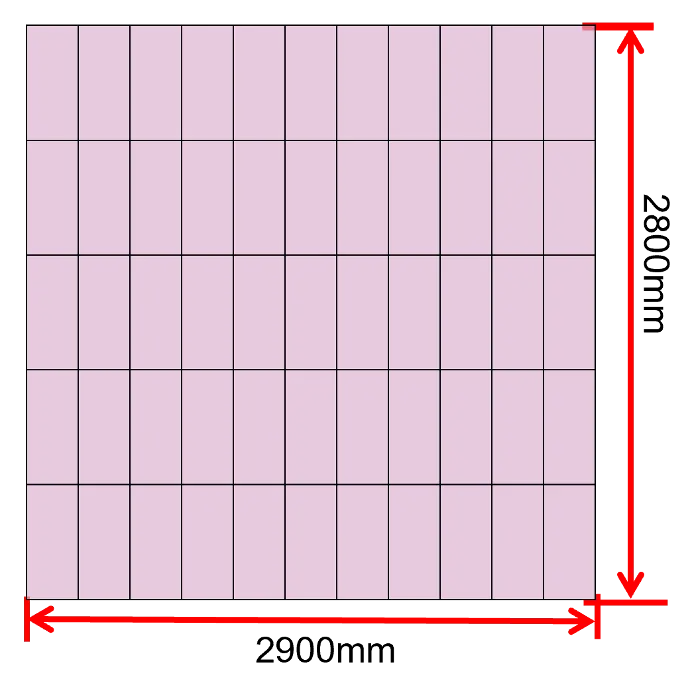
The software is visualized and easy to use
It includes system overview, equipment monitoring, parameter setting, manual operation, debugging operation, stacking planning, IO monitoring, alarm information, statistical analysis, etc., and is the main interface for operating equipment.
Monitoring panel: monitor the signals of the startup conditions, mobile platform, robot, communication diagnosis and other modules, and quickly check the equipment status.
Visual pallet planning: After entering the order information, the software will generate the pallet pattern and display it to the user in a two-dimensional view and a three-dimensional view.
Real-time alarm display: The alarm information panel displays the current alarm content in real time.
Production data analysis: The statistical analysis panel displays the 24-hour status distribution chart of the equipment, and the historical production data can be queried.
Digital twins
The digital twin smart factory builds a fully simulated factory model virtually, and synchronizes the model with the actual factory in real time through real-time data collection, analysis, and simulation. This allows plant managers to conduct various experiments and optimizations through the digital twin system to explore the optimal production concept and process flow without affecting the actual production.
Through digital twin technology, enterprises can achieve personalized customized production, quickly adjust production lines according to customer needs, provide customized products and services, and enhance market competitiveness. In addition, the digital twin can also be remotely monitored and operated, enabling remote maintenance and management, and reducing manual inspection and maintenance costs.
Digital twin smart factories are an important trend in the future of manufacturing development, which will lead to more efficient, smarter, and more sustainable production methods.
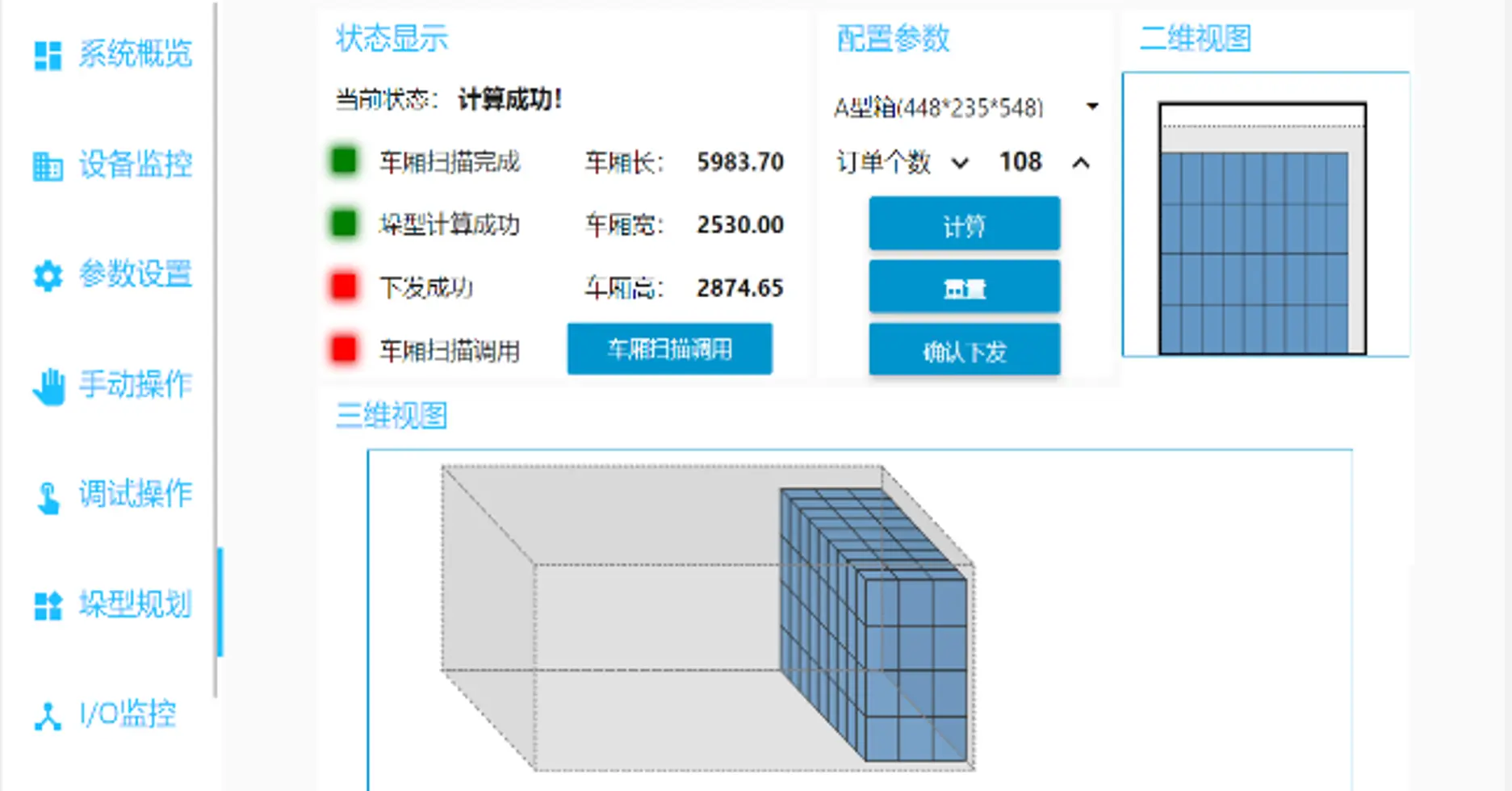
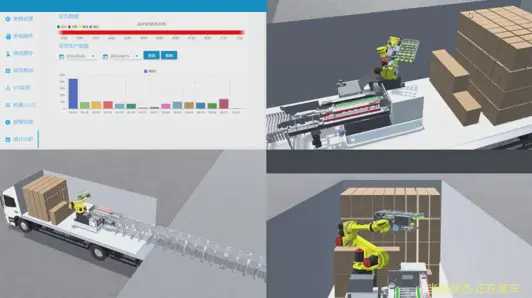
Easy to install and deploy
No need for platform modification: The equipment can be directly applied to the platform with a tilt loading platform, and there is no need to modify the platform with a height difference of less than 40 cm between the platform and the truck.
Conveyor line docking
It can be docked with the main line by means of a telescopic roller line
It can also be docked with existing telescopic belt lines
Power supply: Three-phase five-wire industrial electricity can be connected to the tail of the conveyor line.
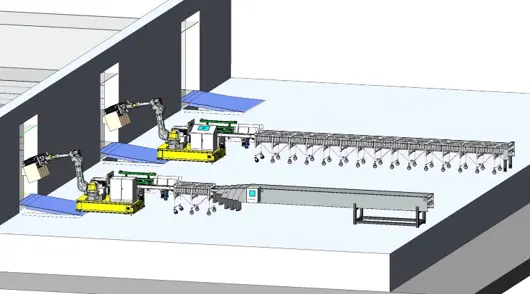
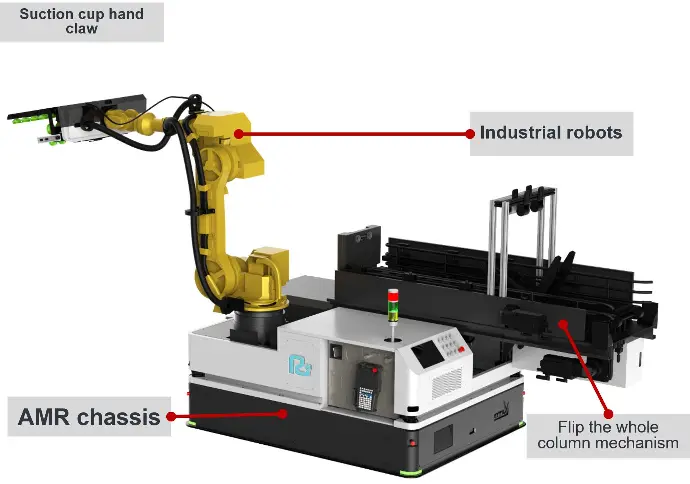
Product parameters
- Products include AMR chassis, robots, hand claws, and flipping mechanisms
- Products size:3.2m 1.5m 0.5m
- Load: Maximum gripping weight 60kg
- Accuracy: The positioning accuracy of the car body is ±30mm, and the stacking accuracy is ±5mm
- Movement performance: can move in all directions, the maximum speed is 500mm/s
- Endurance: Both AMR and industrial robots are powered externally, which can ensure 7 24h continuous operation
- Safety protection: obstacle avoidance radar, emergency stop, indicator light
- It is suitable for cargo loading and unloading scenarios of vans and containers

Application examples
The composite robot loading system is oriented to the van truck or container scene, and realizes the destacking and palletizing of regular box goods.
The system has been verified by domestic head customers, and the equipment performance is stable, which meets the needs of the production line, and effectively solves the problem of labor shortage in this job.
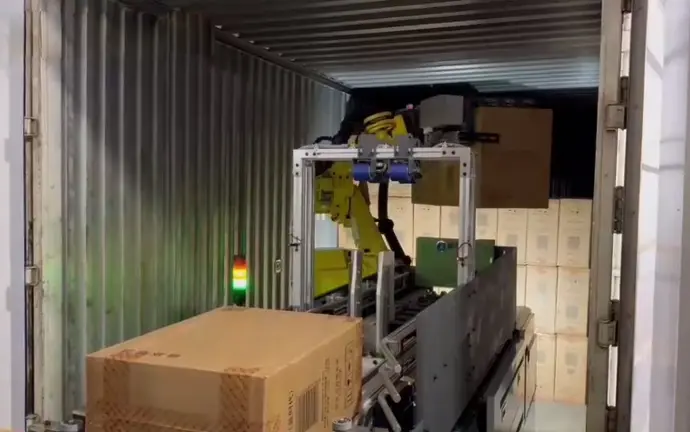
To install this Web App in your iPhone/iPad press
and then Add to Home Screen.